What is the difference between casting and forging
Casting is a process in which the metal is melted into a liquid that meets the requirements and poured into the mold, and the castings (parts or blanks) with predetermined shape, size and properties are obtained after cooling, solidification and cleaning. At the same time, it has wide adaptability and good comprehensive mechanical properties.
There are many kinds of casting, which are customarily divided into:
(1) ordinary sand casting, including wet sand mold, dry sand mold and chemically hardened sand mold.
(2) Special casting, according to the molding materials, it can be divided into two types: special casting with mineral sand and gravel as the main molding material (such as investment casting, mud mold casting, casting workshop shell mold casting, negative pressure casting, full mold casting, ceramic mold casting, etc.) and metal as the main mold material (such as metal mold casting, pressure casting, continuous casting, low pressure casting, centrifugal casting, etc.). Forging is a processing method that uses forging machinery to exert pressure on metal billets to produce plastic deformation in order to obtain forgings with mechanical properties, shape and size. One of the two major components of forging. The casting looseness and welding holes of metal can be eliminated by forging, and the mechanical properties of forgings are generally better than those of castings of the same material. Forgings are often used for important parts with high load and severe working conditions in machinery, except for simple rolled plates, profiles or weldments.
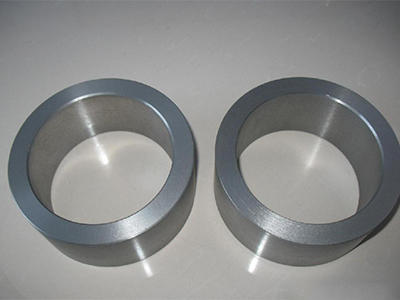
According to the forming method, forging can be divided into:
(1) Open forging (free forging). The metal is deformed between the upper and lower iron (anvil block) by impact force or pressure to obtain the required forgings, which are mainly manual forging and mechanical forging.
(2) closed die forging. The metal billet is deformed under pressure in the chamber of the forging die, which can be divided into die forging, cold heading, rotary forging, extrusion and so on.
According to the deformation temperature, forging can be divided into hot forging (the processing temperature is higher than the recrystallization temperature of the billet metal), warm forging (lower than the recrystallization temperature) and cold forging (room temperature). Forging materials are mainly carbon steel and alloy steel, followed by aluminum, magnesium, titanium, copper and their alloys.
The original state of the material is bar, ingot, metal powder and liquid metal and so on. The ratio of the cross-sectional area of metal before deformation to the cross-sectional area of die after deformation is called forging ratio. The correct selection of forging ratio has a lot to do with improving product quality and reducing cost.
Differences in performanc.
Casting: molten liquid metal fills the mold cavity for cooling. Air holes are easy to occur in the middle of the parts.
Forging: mainly formed by extrusion at high temperature. The grains in the parts can be refined.
Forging: by means of hammering, etc., to make a metal material in a plastic state into a workpiece with shape and size, and change its physical properties.
Casting: metal is heated and melted and poured into a sand mold or mold and cooled and solidified into utensils.
During forging, the metal undergoes plastic deformation to refine grains and cut fibers continuously, so it is often used in the manufacture of important parts, such as shaft, tooth theory and so on.
Casting has requirements for processed materials, and the casting properties of general cast iron and aluminum are better.
Casting does not have many advantages of forging, but it can produce zero with complex shape, so it is often used in the manufacture of supporting parts with low mechanical properties.
For example, machine tool shell and so on.